This article will briefly explain moulding knives cutter head hook angles, and what to expect when using different degree hooks angles while milling lumber into mouldings. We will be discussing the two most common hook angles used in the industry, 12-degree and 20-degree.
Hook angles machined into moulding cutter heads is the degree of which the moulding knife cuts the lumber that is to be milled. Cutter head hook angels come in many different angles depending on the manufacturer. Small changes in the hook angle, sometimes just a few degrees can make a significant difference in the finish product of milled lumber.
Many cutter heads are marked or stamped with the hook angle on the side of the cutter head. The exact hook angle of the knife slots or knife pockets in a cutter head is quite easy to determine if yours are not marked. Use the straight edge of a ruler, and with a pencil draw a straight line from tip of one moulding knife to the tip of the opposing moulding knife in the opposite side of the cutter head. Use a protractor to measure the angle between the line drawn on the moulding cutter head and the face of the knife as shown in the diagrams below.
For many years there has been somewhat of a myth that a lower 12-degree cutter head's sole purpose was to mill hardwood lumber, while a higher, 20-degree cutter head's only purpose was for milling softwood lumber. We will discuss both pros and cons of each hook angle and leave the decision to you on which solution is superior for your milling applications.
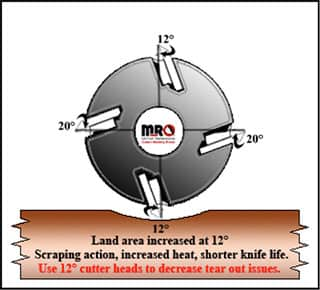
The biggest asset about using 12-degree hook angled cutter head is that they generally eliminate tear out issues in your milling process, which will greatly improve your yield in production and your reputation as a quality mill.
Because a lower angle, a 12-degree cutter head uses more of a scraping method against the wood, it also has longer land time on the lumber per revolution of the cutter head. It will create more friction and cause heat buildups that will dull your moulding knives quicker. In addition, using 12-degree hook angled cutter head could require as much as 15% more horsepower while milling, but this mostly depends on the depth of cut and feed speeds in moulding production.
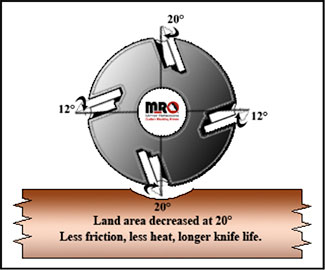
The 20-degree hook angled cutter head has a higher degree of cut. The actual land time of which the moulding knife encounters the wood on a 20-degree cutter head is shorter. This creates less friction, less heat buildup, your moulding knives run times are increased due to less sharpening, and the overall life of the moulding knife will increase while your actual production time will decrease. Moulding machinery with limited horsepower may also benefit from use of the 20-degree hook angle.
Purchasing many cutter heads with different degrees of hook angles can be very expensive for moulding manufactures especially operations of jointed or high speed moulding mills. These types of applications must have the hook angles all the same due to the multiple moulding knives cutting in unison.
For those moulding manufactures of a single knife finish or utilizing low speed moulding machinery you have the less expensive options of purchasing the dual angle cutter head as shown in the pictures above, two knife pockets are machined at 12-degrees and two knife pockets machined in 20-degrees. Purchasing dual angle cutter heads will cost you a little more money than a standard single hook angled cutter heads, but they will save you thousands of dollars over the life of the machinery from not having to buy different angle cutter heads individually. If you run into milling issues, simply change hook angles, sharpen the knives in the different hook angle and solve the issues at hand. Keep in mind you will need filler stock or a blind wedge in the empty pockets while milling; this will keep the cutter head bore symmetrical, eliminating any damage to the cutter head.
In summary, many companies use 20-degree hook angles for all their milling operations unless the run into problems with tear out, then the 12-degree hook angle is a great option, keep in mind moisture content plays a big role in the milling operation and sometimes neither hook angle will solve the issues you might encounter.
If you have, further questions or comments feel to contact us.