What is a draft angle on a corrugated back moulding knife? A draft angle is a slightly tapered line built into the profile and knife design anywhere angles are between eighty-five to ninety degrees on wood molding profiles. These draft angles help maintain the tolerances of the design pattern while milling and allow the knives to be sharpened from the back side of the knife without distorting the tool.
The term “draft angles” in molding knife design is sometimes misunderstood and overlooked and certain types of cutters don’t have the same criteria due to the nature in which they are made and sharpened. There are also many ways knives can be produced for milling wood from MDF (medium density fiberboard) and other composite materials, basic manufacturing on an industrial molder. Here are just a few that come to mind, face ground cutters, carbide insert blades and corrugated back knives. In this article we will be focusing on corrugated back knives. This type of blade will require some degree of draft angle built into the high-speed steel or carbide cutters, but first lets review a few of the other types we mentioned.
Face ground knives are sharpened on the smooth face side on the knife when they become dull, the thickness of the knife will get thinner as time goes on between sharpening. Very little distortion in the profile occurs between sharpening except in the area of the knife that has side clearance ground into the side edges of the profile to help the knives breathe. Side clearance provides good wood chip flow which will also aid in keeping the knives cool during milling. When sharpened there are only a few thousands of an inch taken from the thickness of the blade, so it is generally not a concern. Braised on carbide (Freeborn cutters in image below) are a good example of face ground knives. By the time the carbide need replacing, there is little distortion to the profile because the carbide is roughly one eight to three sixteenth of an inch in thickness.
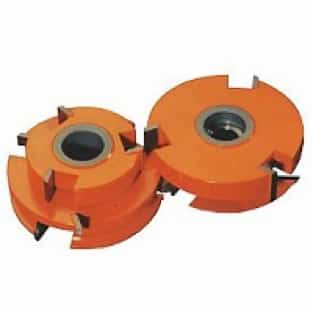
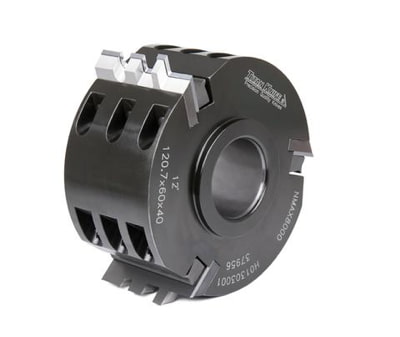
Carbide insert knives like the Titan knives in the image above can have very close to ninety degree inclines built into the design, they can also be sharpened once or twice from the face side of the profile, but in general these types of knives are usually discarded after milling several thousands of linear feet of moulding.
That brings us to corrugated back knives, these are the type of cutters Mirror Reflections manufactures. This style of cutter is always ground from the back side of the steel or carbide blanks , therefore the height of the knife is reduced each time they are sharpened until you reach the designated safety limits on the cutter head, they are then are discarded. They can be sharpened several times without distorting or changing the knife tolerances as long as certain criteria is met.
The images show a simple one-half inch tall by one quarter inch wide dado knife for a cabinet door rail , this is where the solid door panel edge fits into when it is assembled. We chose this detail because it best describes a dilemma we are challenged with while designing the knife: whether to design tooling with or without a draft angle built into the pattern. If we design the knives without a draft angle as shown in example marked “A”, the cutters will not be able to hold it’s dimensions after the initial grind and subsequent grinds will exhibit noticeable differences in knife and wood tolerances. There will also be an increased burning in the knives because there is now more surface area of the knife cutting the wood with every revolution of the tool. This larger contact area of cut surface causes more friction, producing more heat, which in turn reduces knife life, the temper of the steel, and milling time substantially. This is just one of the many reasons most cabinet door manufactures use insert carbide tooling for a dado cut, another reason is that the dado where the flat panel connects becomes out of square from tapered knives with draft angles. This out of square gap between the panel and rail is quite obvious to the eyes of professional artisans.
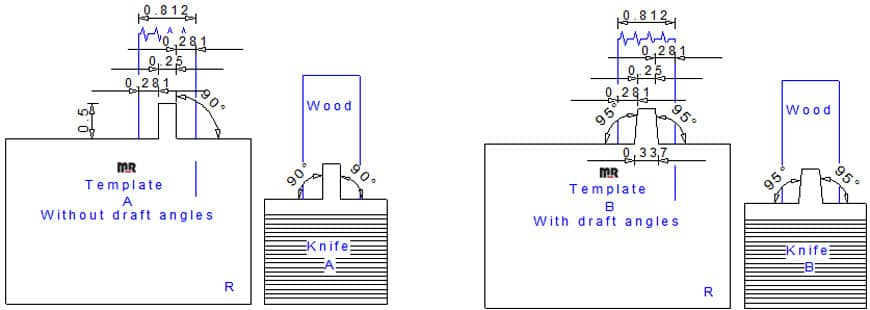
I’ll explain why the knives are unable to hold the measurement tolerances when designed without draft angles. When we back grind cutters as explained above, the height of the knife gets shorter and shorter each time we grind. Say for example we grind .062” off the top and bottom of the knives, the sides of the knife still remain dull on the remaining 7/16” of the incline because the cutters were designed at ninety degrees. Now if the operator who grinds the knives simply moves the axial carrier on the profile grinder enough to sharpen the vertical edge, then the problem is solved right? Wrong, the profile grinder operator just changed the axial constant position resulting in the tolerance of the ¼” wide dado to be smaller by a few thousands of an inch on one side, he then grinds the other side yielding the same effect. Now the knives and the cut in the wood are no longer within tolerances, so the machine operator if forced to offset the knives to be able to mill to the correct sized cut. Offsetting the knives is both time consuming and highly inaccurate unless you have a Weinig Opti stand or other measuring device to aid in aligning the axial measurement on the tool.
All this being said, the cutters in the image marked “B” can be consistently sharpened properly because of the draft angle in the design. This draft angle holds the tolerance at the top, bottom, and more importantly at the sides of the knife! The larger the degree in draft angle you have, the easier it will be to sharpen the knife when it becomes dull, you will also yield longer milling times between sharpening. Most of our knife profiles utilize five-degree draft angles.
The smallest draft angle we recommend is two degrees. Since the knives experience increased burning more steel will have to be removed each time you sharpen. We find draft angles under two-degrees will require the removal of at least 1/16” of the overall height of the knife each time to be able to keep the cutters within tolerance, so basically that results in the blades being able to be sharpened four to six times before you would exceed the safety limits of the tooling as explained earlier. This also explains why it is more economical to invest in carbide insert tooling for the long haul. Investing in carbide insert tooling will reduce the amount of time and money spent on tooling that would otherwise burn wood and consistently be out of tolerance.
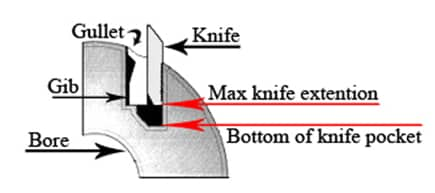
Draft angles come into play more often than our clients realize. When designing corrugated back moulder tooling we utilize these angles everywhere they are required, this is one of the main reasons our moulding knives last longer than most of our competitors. From simple patterns like half round circles to everyday designs like casings or even more sophisticated and complex profiles like picture frames, there should be a five-degree draft angle wherever there is a ninety-degree angle.
This is not some fancy term we made up, it’s actual tooling science and must be adhered to if you want your tooling to last and to be able to be sharpened correctly within tolerances. In the images below there is a blue circle around each area of the profile that requires a draft angle in the design stage, you can clearly see that we pay attention to even the tiniest parts of the detail.
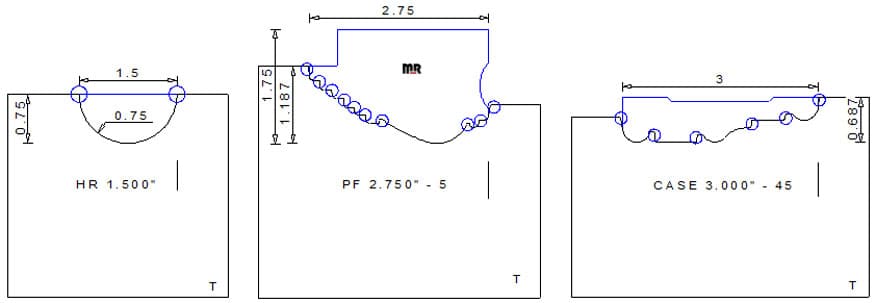
A comment we hear all the time is: “that’s the way the architect designed it, it has to match.” Well as far as we are concerned the designer is very intelligent in their field of expertise, but like everybody on earth, we all have a specific God given talents. We are willing to share our gift with everyone if they are willing to learn, this is the main reason for writing this article, to educate and to help others understand the science built into our molding knives.
Some people may disagree with us regarding draft angles and that’s ok, we back our claims with science. Other folks have us make cutters, then have another company face grind them when they become dull. Afterwards, they notice a considerable decreased in milling times between sharpening. Troubled, they send the knives back to us to try to have them fixed. Sadly at this point we are unable to help them because most of our high speed steels are coated or heat treated on the surface (face side) of the knives to reduce friction and heat. If you face grind the knives, you grind away the hardest part of the knife. It’s no wonder why you can’t hold an edge on the blades. On top of that, face grinding corrugated back knives leaves a lip on the face side of the knife. This lip gets hung up on the tool rest of the profile grinder during sharpening making accurate sharpening impossible.
The bottom line is, if you have corrugated back profile knives, they must be sharpened and maintained the same way they were initially ground.
There are indeed certain circumstances where a ninety-degree knife is necessary, take for instance rabbet knives on panel molds, wall caps and backbands. As discussed with the dado knife above, if it were left at ninety degree it would burn and not be able to be sharpened properly without changing the profile. Rabbet knives only have one side of the cut, not two like the dado design, so in theory only one edge would burn. In this circumstance the profile grinder machine operator can move the axial position on the template carrier to sharpen that edge. It would alter the constant position, but this can easily be compensated for on the molder’s axial positioning. The axial position will change every time the knife is sharpened, burning on the wood and knives is eminent but this can all be minimized with five to ten-degree side clearance ground into the vertical incline of the tool.
That concludes our article on draft angles in corrugated back moulding knives, if we can be of any further help, or if you have a few questions or comments about the information please feel free to contact us, we would be happy to assist you.