This topic of moulding cutting circles is a guide on minimum and maximum cutting circle parameters for cutter heads used on wood moulding machinery. We will easily and thoroughly explain how to determine the cutting circle for maximum efficiency on your moulder machinery.
First let us start with the definition of a cutting circle; the cutting circle equals the total diameter of moulder spindle shaft, the cutter head, and the moulding knives furthest tip extended out from the cutter head. Some moulding machinery on the market today do not have spindle shafts, this type on machinery the cutter head is the spindle shaft but the equation is exactly the same.
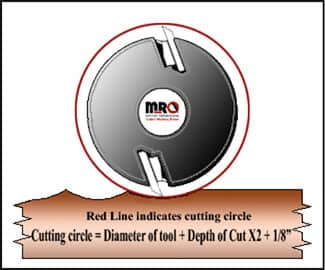
Every moulder spindle on your moulding machinery has a minimum cutting circle and a maximum cutting circle, it is very important for you to know the limits of each moulding spindle on your machinery. You should be able to find your specifications of your particular moulder in your owner’s manual, read these manuals many times, they are loaded with a lot of very important useful information. If you do not have an owner’s manual, please contact the manufacturer they will be happy supply you with one.
We know quite a few cutting circle specifications on moulding machines you currently use in production from our years of experience, but the industry is changing all the time, we cannot be expected to keep up with all the changes that are made by various moulding machine manufactures. We recommend you read our article on cut steel sizes for moulding knife blanks ; this will play a significant role in how to obtain a clearer understanding regarding your moulders cutting circles.
Initially, we will focus on the minimum cutting circle; this parameter involves the smallest diameter cutting circles. It involves items such as cutter head diameters, moulder fences, chip breakers, guides, and pressure elements currently installed on your moulder. If your cutting circle were too small, you would be unable to adjust these items listed above to the proper settings suggested by the manufacturer. The main cause of an undersized cutting circle is the use of smaller diameter cutter head than recommended by the manufacturer of you machinery. However, a smaller diameter cutter head may become an asset when it involves the maximum cutting circle and its parameters.
The maximum cutting circle on your moulder is the issue that we should be more concerned about, this is where the larger depth of cuts come into play. Components on your machinery such as chip breakers, pressure elements, fences, and spindle housings would be obstructive; this would keep you from being capable of completing the swing on the moulding knives. The issues listed, could compromise operator safety, lead to moulding knife breakage, as well as damage to your moulding machinery from exceeding parameter guidelines.
We will work with you to determine if we can distribute the total depth of cut between two or more cutter heads. These changes will reduce the cutting circle, close up bedplates, chip breakers, and fences while keeping your knives within the manufacturer's guidelines. Please read our article on moulding profile template design. moulding profile template design . This article will give you a better understanding on how we handle larger cutting circles.
Please use the following information to determine the largest depth of cut your moulding machine is capable of manufacturing within the parameters of the machine, keep in mind you will have to determine this for each moulding spindle on your machinery. This information should be known by the moulder operator and shared with the knife grinding room, sales staff, and anyone involved with bidding or quoting before any manufacturing process begins. We would not want to begin a job if we have no way of ever being able to swing the moulding knife to run the product desired.
Here is an example of a, 7-7/8” cutting circle for the top spindle on your moulder. We know this is a common maximum cutting circle for many moulding machines in the field, know exactly what your cutting circles are. For demonstration purposes, we will a 1-1/4” depth of cut as our example. Please keep in mind, most if not all, corrugated moulding knife steel is 1/16” between each corrugation. Basic math skills apply here, anybody can figure this out, you must be aware of all your moulder machines cutting circles limits.
- 1.250” Depth of Cut X 2 (we need the diameter) = 2.500”
- Add the diameter of your cutter head, let’s use a standard size diameter for a 1-1/2” bore cutter head, which is= 4.812”
- Add at least 1/8” (.125”) to the equation, 1/16” for each knife corrugation, X 2 knives, reason, you would never have the knives flush with the outside edge of the cutter head.
2.500” Total Diameter of Cut + 4.812” Diameter of Cutter Head 1-1/2” Bore + .125” So Knives are not flush with Outside Diameter of Head _________________ = 7.437” Total Cutting Circle
You can plainly determine, you would be able to run this product on your moulder spindle with a cutting circle of 7-7/8”, you would actually have .218” of clearance left over.
There is a lot of information that comes into play when designing a moulding to run on moulding machinery, this is just one of the challenges we face on a daily basis. We hope we have provided you with a better understanding about cutting circles for moulder’s and how they play a vital part of your milling operation. If you would like further assistance, please contact us.