This informational article is for moulding machine operators requiring assistance in solving common finish issues that involve improper hold down on wood mouldings that may occur during the milling process.
As moulder operators we are all faced challenges that we have to deal on a daily basis, we are going to help you understand how to make a simple, but effective custom moulding pressure shoe to install on your moulder.
As moulding designers, we always attempt to supply you with favorable areas for hold down while milling, unfortunately, sometimes we must create moulding designs that have unfavorable hold down requirements; different elevations in the design force us to fabricate a custom pressure shoe or to outsource to a more expensive, custom pressure shoe manufacturer.
Below are some thoughts on how to design a custom pressure shoe, you may have other solutions that work, but this is just one step by step process that we’ve established, and have determined works quite well.
Expect the first few pressure shoes you make to take a little more time to produce, your comfort level will increase by the time you build a half a dozen or so. Our intensions are to design an operational pressure shoe that is easy to build, develop your confidence, while you save you money and time from purchasing aftermarket products that leave you waiting and depending on others to help solve your moulder finishing issues.
Select a piece of hard rock maple that is thicker and as wide as the thickness and width of the current metal pressure shoe installed on your moulder, then rip a six feet or longer piece of lumber on your table saw, the longer the board the more pressure shoes you can manufacture from that board.
Purchase or find some 1/32” or 1/16” thick plastic laminate, you probably already have some lying around the shop; cut two pieces of laminate the same width as the maple board.
Measure the thickness of your original metal pressure shoe that is installed on your moulder; plane the piece of maple on your planer to the exact thickness as your pressure element, minus the thickness of two pieces of plastic laminate, one for each side of the board, use contact cement for adhesion. The laminate will make the pressure shoe smooth, and responsive like the original metal one. It should last for years, and the nice thing is, you will never have to worry about calibrating the pressure shoe mechanical counter every time you change from the custom pressure shoe to standard pressure shoe
Take the board over to the table saw and cut a bevel on both edges of the long side of the board, use the same bevels that are on your original metal pressure shoe using it as a MoulderPressureShoeCustomMade to cut the correct angles. This will allow you to get the pressure shoe closer to the moulding knives when adjusting the cutting circle during set up procedures, while simultaneously creating enough room for movement of the out feed rollers on the moulder. Make sure to sand the leading edge so it is blunt, not sharp, allowing the shoe to receive the moulding smoothly, this way the shoe is not caught on any lumber while milling. Use paraffin wax on the ends where mitered cuts were made, this will eliminate any moisture that may absorb into the end grain from seasonal changes of humidity, this could cause the pressure shoe to warp or cup over time.
You now have the ability to make several custom pressure shoes depending on the length of the board you originally made. Measure and cross cut a piece of the board with a chop saw, to the size of the moulding being milled or wider ,this way you have the ability to use two bolts for securing the pressure shoe to the mounting bracket when ready.
Go back to the table saw, cut a dado into one side of the wooden pressure shoe, the same size width and depth as the keyway located on the bottom side of the mounting bracket that holds your original metal pressure shoe in place. Check the fit of the mounting bracket in your milled dado; make sure it slides smoothly and freely just as the metal one does. Use a drill bit and predrill two holes so you can secure the pressure shoe to the mounting bracket, small lag bolts and washers work well, get them in millimeters to avoid the use of special wrenches just for the pressure shoe.
It is extremely important on exactly where you predrill the first hole, make sure the lag bolt bottoms out at the end of the slot located in the mounting bracket, this way it does not allow the pressure shoe to travel laterally, beyond the inside fixed fence of the moulder. Preferably, make it so it stays away from the inside fixed fence by about a 1/32”, that way you never get hung up on the fence when lowering the pressure shoe into positions of smaller thickness dimensions.
Ok, we have just a few more steps, you are doing well, it seems like a pain in the butt, but once you make the first one and see how well it works you will be glad you invested the time into a longer sized board.
Rip and plane some maple strips about one and one half inches wide by three or four feet long to various thickness on your planer, do not go smaller than one quarter inch thickness, you probably will not need it.
The final steps, measure the distance vertically between the flat surfaces marked by X’s on the diagram (.299”) of the moulding you are making the pressure shoe for to the spot on the moulding (preferably flat) that you could hold down on. Rip one of the preplanned strips you made earlier one half inch wider or so than the difference in elevation of the moulding, this is concealed within the dado you make next. Measure the distance from the edge of the moulding horizontally (.855”), to the spot on the moulding you want to hold down on, see example below.
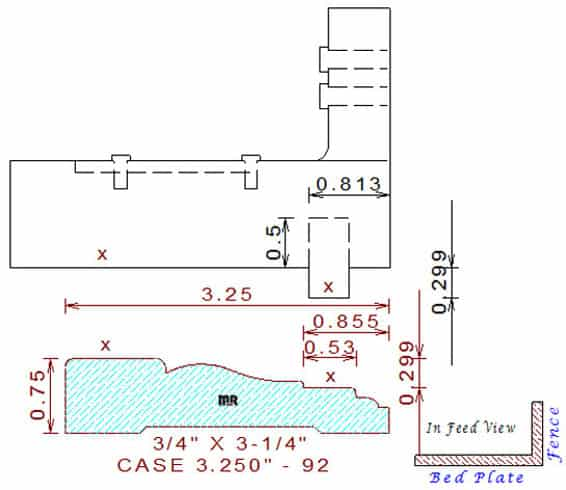
Take the pressure shoe back to the table saw, cut a dado into the pressure shoe, the opposite side of the dado you milled for the mounting bracket. Referring to the example above, measure 13/16” (.813”) from the edge; do not go wider than .855” or it will interfere with the next upward step in the moulding design.
Make the slat a 1/2” wide by 13/16” tall or larger; we will trim it on the table saw to the exact size after gluing it into the dado. Cut it longer in length the than the total length of the pressure shoe, this will enable you to get that part of the custom pressure shoe really close to the moulding knives while eliminating any chatter, from poor hold down design.
Place a little glue into the dado then insert the precut strip into the dado, place a few clamps to hold in place while the glue dries, one hour should or so be good, but overnight would be perfect.
The final step: back to the table saw, stand the custom pressure shoe on edge and cut the extension to the exact size needed, in this example above it is .299”. Chamfer the front and back leading edges of the extension for the same reasons listed above, lightly sand the saw marks to make it smooth, and then secure it to the mounting bracket.
Good job, you have successfully made your first custom moulding pressure shoe, now you have even more knowledge about running some of the finest mouldings your clients have ever laid eyes on, we were happy to play a role in your success.
One last note: make sure you keep your last bottom moulder knives really sharp, dull moulding knives here can transmit finish problem into the moulding no matter how well you hold down the moulding.
Please read our article on moulder pressure shoe calibration , if we can be of any further assistance, please give us a call, we would be delighted to help you thrive in all your moulding encounters.