In this article, we will provide a thorough explanation, along with a diagram on how to properly align the axial positioning of both the horizontal and vertical spindles on an industrial style moulder.
If you have ever removed a moulder spindle from it's cast housing on your moulder for cleaning or repair you may find that it can be a little tricky to realign the cutter head spindle assembly correctly to the bedplates or fixed fences on the equipment.
We would like to provide you with tips on proper moulder spindle alignment that will save you time, as well as provide you with the knowledge you need for future maintenance on your machinery.
The first thing we will address in regards to the alignment is the reference points. There are two referenced zero points on your moulder from which these spindles are aligned to, all axial and radial measurements begin at these two locations on the moulder. Some of these numbers are positive, and some are negative but your measuring counters located on your machinery will show them all as positive numbers. The first zero reference point is located on the fixed fence, it is on the inside of the machine for the horizontal spindles axial movement and for the vertical spindle radial movement. The second reference point is located on the bedplate for the vertical spindles axial movement and horizontal spindles radial movement. For adjustment of these individual spindles, please refer to our articles on axial and radial calibration procedures.
When replacing the spindle in the cast housing, make sure the housing is clean and clear of any debris and bring the axial collar flush to the back side of the casted spindle housing by turning the axial crank on front of machine; this will make it easy to insert the spindle without binding or damaging the axial collar. Inserting the spindle from the front or rear of the machine is a personal choice however, I prefer to insert the spindle from the front on the machine. In my opinion this makes it a little easier.
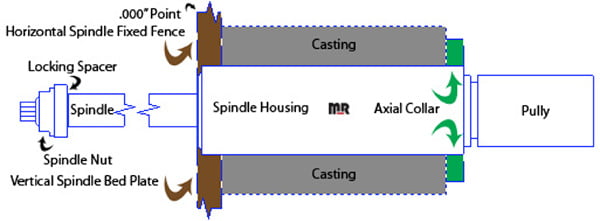
There are two axial collars designs that secure the axial adjusting collar to the actual spindle housing. The first style wraps around the back end of the spindle with a single hex bolt to tighten it. These types of collars tend to jump around during operation if the housing is not well lubricated. With the second type of axial collar design the spindle bottoms out inside the axial collar itself. This type of collar will have six or eight holes for bolts on the backside to secure the spindle to the axial collar. This type of collar is superior for axial movement because it lessens the chance for binding while adjusting your spindle axially. The drawback to this type of collar of course is that it is more difficult to line up the holes to secure the spindle to the collar itself. However, I will explain how a small flashlight can assist with the alignment when installing spindle into housing and axial collar for this type of assembly.
Once you have the spindle inside the cast housing the style of axial collar you will have to change the alignment sequence a bit depending on your particular collar. If you have the type with the holes for bolts at the bottom of the spindle and in the collar itself, secure them with the allen hex bolts once you have the holes aligned. If you have the wrap around style with a single hex bolt leave it loose for now until we align the spindle to the inside fence of the machine.
To align the spindle simply wedging a ten-inch straight edge between the base of the spindle and a sixty-millimeter spacer on the spindle shaft from your machinery; this is the zero point on both the spindle base and where you install the knives into a cutter head. With the axial collar flush against the casting move the spindle by hand so that it is even with the inside fence. Use a small flashlight placed behind the straight edge to help you know when both are aligned. The light will dissapear when they are properly aligned. Next, lock the hex bolt that tightens the axial collar around the spindle and set your axial counter to .000”.
The previous step ensures that the axial movement does not go beyond the fence. Beyond the zero point there would be no knives, or cutter head, and in all actuality the numbers you see displayed on your counters are negative numbers. So the axial constant, which is 10 millimeter or .394 inches, is the exact location of the base on the moulding spindle, positioned .394” behind the fence, or below the bedplates if you were referring to a vertical spindle.
Congratulations! You have successfully aligned the cutter head spindle, you will have a full range of axial moment exactly as the manufacturer intended for your moulding machine, but we have one last task to complete that will allow for easy positioning of your axial for months or years to come.
Let us look at the cast housing you placed the moulding spindle into, look for about a ¼” wide slit or cut in the casting going the full width of the casting, this gap was machined for the sole purpose of allowing movement of the spindle during set up and locking the movement during operation. Unfortunately, this gap is a resting in a place where wood chips, that are flying around while milling lumber can get stuck. They wedge themselves into the cast housing and eventually restrict the axial movement. However, there is a very simple remedy, by taking your grease gun and filling the gap with grease you can keep the axial movement of your spindle free and clear of debris for a very long time. Instead of getting stuck in the slot, the wood chips stick to the outside of the greased slot which is much easier to clean. Although I don't recommend using compressed air at these greased locations, trust me you will have a mess.
After completing all task listed above, reinstall the belt onto the pulley and motor, and tension properly. Install all safety devices to their proper locations and you should be good to go! We realize that there may be moulding machines that have different criteria for axial spindle alignment, this article is intended for general information, it is always best practice to refer to the manufactures intended alignment procedures.
Well that completes yet another article specifically designed to assist you with your industrial moulder, if you follow a regular maintenance program you will find that the axial movements will be properly aligned, free of debris, and easy to adjust, making your job easier and you more productive! If you have any further questions please feel free to contact us.