This article about moulding knives grinding procedures devotes itself to all the professional grinder men and women in the moulding industry. I feel privileged to have worked with, as well as trained under some very talented craftsmen while performing my duties as a service technician, grinder man, and moulder machine operator. Over years of training, exchanging information, trials and many errors, success has steered us to share this information with all of you, in your quest for higher level of professionalism within our trade. You may also want to review our moulding knives videos to help better understand the in depth information in this article, the person explaining has a different accent, but that depends on what part of the world you live in.
Following the moulding knife grinding process below, along with high quality knife grinding machinery will permit you to grind professional grade moulding knives on your own, in no time at all. Remember, everyone that produces moulding knives has had their first day grinding, be patient, it will come in time, but most of all relax, the more knives you grind the easier it will become.
Keep in mind these moulding knife-grinding steps is a general information guide, this information is obtained in schools of trade, collages, manufacturers of moulders and profile grinding machinery, service technicians in the field, and people like us. You might want to experiment with rpm speeds, grinding angles, and different styles of grinding wheels, for your own personal style of grinding, but these methods and procedures work quite affectively.
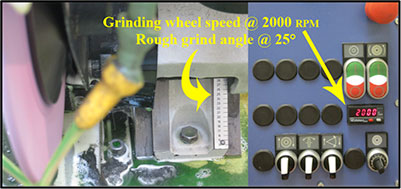
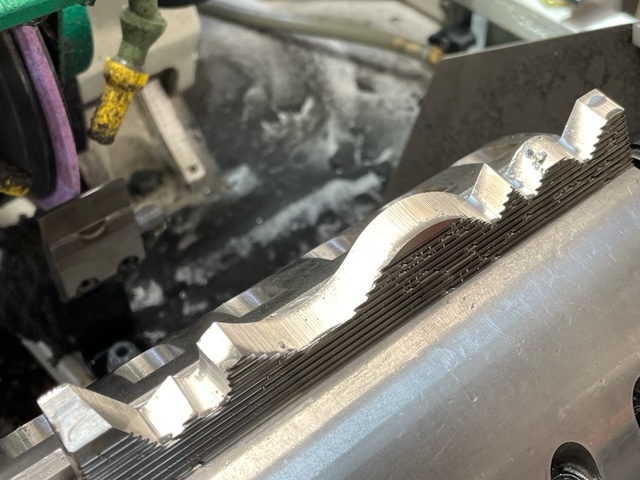
High Speed Steel Rough Grinding Process
- Install rough grinding wheel on your profile grinder (54 – 60 grit size), then set back clearance-grinding angle at 25 degree.
- Set a proper distance of .020” between the wheel and the tool rest, simply use a feeler gauge until you get it mastered. This 020” setting is the center of the circle of which you get your correct back clearance angle degree.
- Set grinding wheel speed between 1800 - 2000 rpm depending on the diameter of the grinding wheel.
- Make sure grinding wheel width matches the tracing pin. A good practice is to dress the rough grinding wheel between 3.7mm - 3.9mm while using a 4mm round tracing pin. The reason being, it leaves a little extra steel for the finish grind process while compensating for your grinding wheel going square during the rough grinding procedure. Use of a square tracing pin can lead to damage of the plastic template if you are not careful. Reserve your square 4mm tracing pin for rough grinding carbide applications.
- Index moulding knives to highest point of template by moving radial template carrier, now check the other knife to make sure they are in the same position in the cutter head.
- Rotate the cutter head to a position where there is no moulding knife in play. Bring the cutter head carrier to the lowest point of the template; (do not move the radial adjustment). We are just making sure you have the moulding knives extended out far enough out of the cutter head so you will not be grinding into the cutter head, refer to our article about cut steel sizes for moulding knife blanks .
- Turn coolant and grinding wheel in the on position, rough grind knives until the tracing pin contacts the template.
- Index the grinding wheel toward the tool rest for proper distance of .020”.
- Regrind the knives again until you hear the grinding wheel touch all the way thru on all knives. (You are compensating for wheel wear by doing this).
- Dress grinding wheel often with wheel dresser stone to maintain a round shape similar to the tracing pin. Regrind all knives while maintaining the proper distance, between the wheel and the tool rest. .020” (doing this keeps you angle correct).
- Set your side clearance to 5 degree on any incline angle above sixty degree, grind in all areas needed, (you are still at the rough grind angle.)
- Redress wheel (round). At 0° side clearance, regrind all knives while maintaining the proper wheel to tool rest relationship at .020”
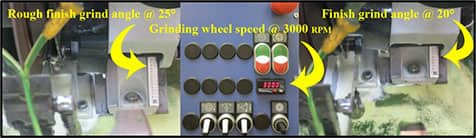
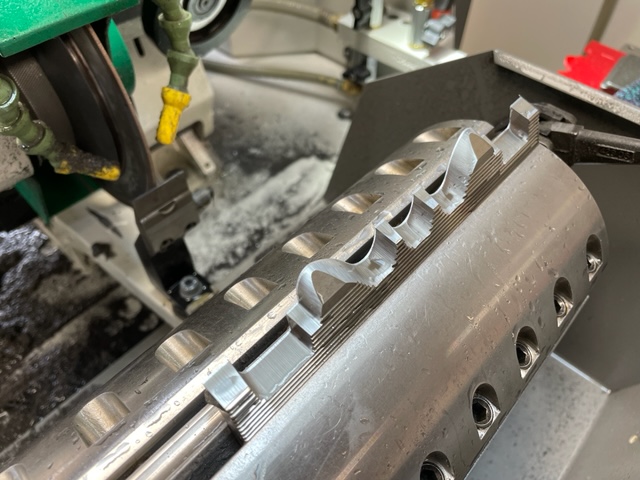
High Speed Steel Finish Grinding Process
- Install finish grinding wheel on grinder, keep back clearance-grinding angle at 25 degree for now.
- Always set finish-grinding wheel @ 3000 rpm (Recommended 120 grit 125% concentration borazon wheels to get best finish).
- Keep a constant distance between grinding wheel and tool rest at .020”.
- Make sure that you check the wheel & tracing pin to match exactly.
- With grinding wheel and coolant in off position, index wheel towards knife until you make minimal contact.
- Turn water and wheel on, grind over all the knives taking off very little. A 2mm tracing pin and wheel will allow you to get in all the tight spots that the 4mm grinding wheel did not allow you in. This extra step will smooth out and remove the rough grinding marks, allowing for smoother wood chip flow during moulding production. This tip will keep your moulding knives cooler during the milling process and the moulding knives will last longer between sharping.
- Place side clearance (tilt grinding wheel) at 5 degree on any angle over sixty degree, grind knife in all applicable areas.
- Finally, change back clearance grinding angle to 20 degrees. With coolant off and grinding wheel on 3000 rpm, index template carrier towards grinding wheel until you made minimal contact with knife steel (go by sound). The finish grind should have about .015” -.020” heel on the moulding knife, smaller is better. Now turn coolant water on and proceed to grind finish grind over all the knives.
For grinding operations that use carbide, weather inlaid or solid, back clearance and finish grind angles will change slightly to 23 degree on the rough grind and 18 degree on the finish grind. The rough and finish grinding wheels will change to Diamond on the solid carbide and CDX on the inlaid (TCT) style carbide.
Our goal is that we provide an in depth understanding of moulding knife-grinding procedures, please contact us if you need further assistance.