In this informational article, we will examine the significance of proper leveling and vibration stabilization for a Weinig R960 profile knife grinder. These duel procedures will benefit all makes and models of profile knife grinders manufactured while increasing the service life of the machinery.
Mirror Reflections has owned and operated seven Weinig R960 profile grinders throughout the years. The quality and accuracy of Weinig machinery has been a consistent second to none machine after machine. Many subtle changes in the manufacturing of the profile grinder has taken place over the last thirty years, while some changes were very good, a few were not as welcomed. There have been some vibration issues with the coolant pumps that have been addressed and fixed with a stabilization pad placed between the pump mounting bracket and the coolant pump base, if you are experiencing this phenomenon contact the Weinig service department for help.
Weinig started using a new style of grinding wheel motor in the last few years, as far as we can tell it happened around 2013 -2014. The motor is a little bigger in size and runs at a higher pitch frequency when grinding than the older quieter motors of days gone by. We feel the company is always trying to improve the quality of their machinery, which is the main reason we choose Weinig for our profile knife grinding needs.
We recently installed our newest profile grinder in the summer of 2019, I noticed the wheel motor having minor harmonic vibration between the speed range of twenty-seven hundred and three-thousand revolutions per minute. These slight issues caused the rough and finish grinds to retain tiny ripple lines in the knives, depending on side to side traverse rate of the axial table while grinding. You could take your fingernail edge and feel the ripples as you go across the ground surface of the knife. These 3000 rpm wheel speeds are primarily used for borazon, diamond and cdx wheels, this high speed and discipline contributes to the paramount quality of all our profile knives.
As a former Weinig technician we were always taught to use proven trouble shooting methods as well as new solutions to help solve glitches in the field. I got to thinking about how to reduce the vibration between the motor and frequency drive, I made a few adjustments in the parameters of the VFD but still was not satisfied with the results. Time to do a little online sleuthing about machine vibrations caused by harmonics in the VFD. I found a company named AirLoc , the more I read, the more I knew they could help me with my issue.
AirLoc has many vibration reducing options on their website, I was overwhelmed with what I really needed to help eliminate my vibration issue, so I contacted the company and was put in touch with one of their product engineers. They asked questions about our machinery including weight, height, width and the number of leveling feet on the machine. They also wanted to know, at what rpm speed were we experiencing the most vibration. After many calculations the engineer came up with a special leveling pad and cushion configuration for our Weinig R960 profile grinder. I purchased a set of four pads and placed them underneath the original cast pads that came with the R960, then leveled the machine as described below. I am happy to report the minor vibrations I was experiencing was eliminated with these pads in the picture below. If your experiencing a similar issue with minor vibrations, we can offer you a few solutions to help.
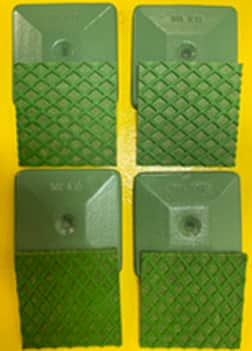
This set of four cast leveling pads measures 4-1/4” square, 13/16” thickness including the pad on the bottom. They have a 3000 lbs. weight limit, (Weinig R960 profile grinder weighs under 2000 lbs.) Set of four cast leveling pads $110.00.
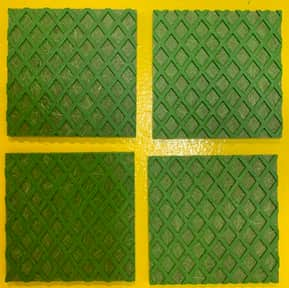
This set of four cushion pads are installed under the original Weinig cast leveling pads. They measure 4” wide by ¼” thickness and have a 3000 lbs. weight limit. Set of four pads $50.00.
Now that we have the minor harmonic vibration issue solved let’s proceed with some brief explanations of why profile knife grinding equipment should be leveled prior to use, and periodically checked during the lifespan of the machine.
The lineal bearings under the table allows both radial and axial movement of the grinding arbor carriage, this area can be affected and eventually cause flat or dead spots in the roller bearings and cage’s themselves if the machine is not level. Lineal bearings can be expensive, they require an experienced service technician to be properly aligned after being replaced.
Dovetail slides are another thing that comes to mind, these cast iron slide ways enable the grinding machine to change back clearance knife grinding angles, they can be worn prematurely causing differences in rough and finish grinding accuracy over time, these slide ways are also very expensive and time consuming to replace.
Proper water filtration is essential on knife grinder machinery, water seeks its own level, a profile grinder that is not leveled properly will hinder the machines ability to filter and reuse the grinding coolant water.
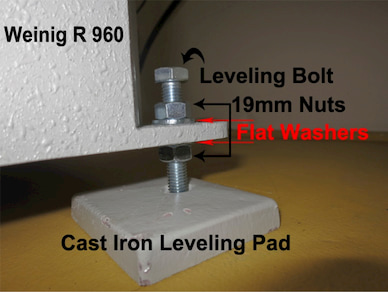
Most moulding knife grinders come with four leveling pads made of cast iron to help absorb minor vibrations, four 19mm leveling bolts, eight flat washers, and eight 19mm nuts to secure the leveling bolts once the machine is level. The image located above illustrates the proper assembly of a single leveling bolt and leveling pad on one of four corners of a Weinig R 960 profile grinder.
Starting with placement of the Weinig R 960 on a hard, stable surface, preferably cement, all knife grinding equipment ought to be level in both directions front to rear, and side-to-side to obtain proper functionality of the equipment in service. When beginning to level the machinery choose one direction first, front to rear or side to side, making sure all leveling bolts carry equal amount of weight load. A quality machinist level is required to perform the leveling task efficiently; a duel level (levels in both directions at once) works best to reduce the time it takes to accomplish the job.
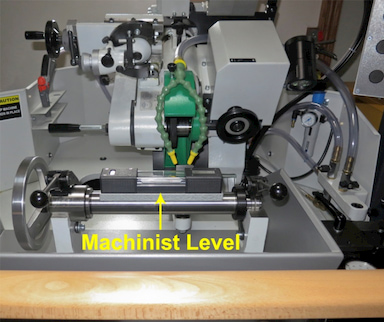
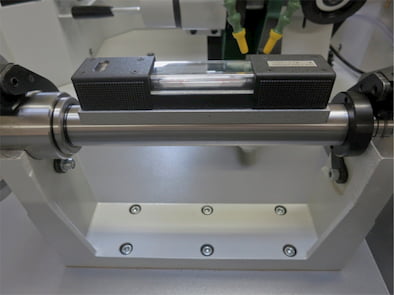
Place a grinding spindle arbor in the carriage assembly, clamp into place, next place the machinist level on top of grinding spindle as illustrated in image above, then adjust the leveling bolts on one side or the other depending on which movement is required to obtain levelness.
The images above illustrate an excellent area for leveling the machine from front to rear, place the level up against the tool rest-mounting bracket, this area is the most desirable section of the sheet metal water-recycling tray, next adjust leveling bolts located in front or behind machine depending on which direction you need to adjust to levelness.
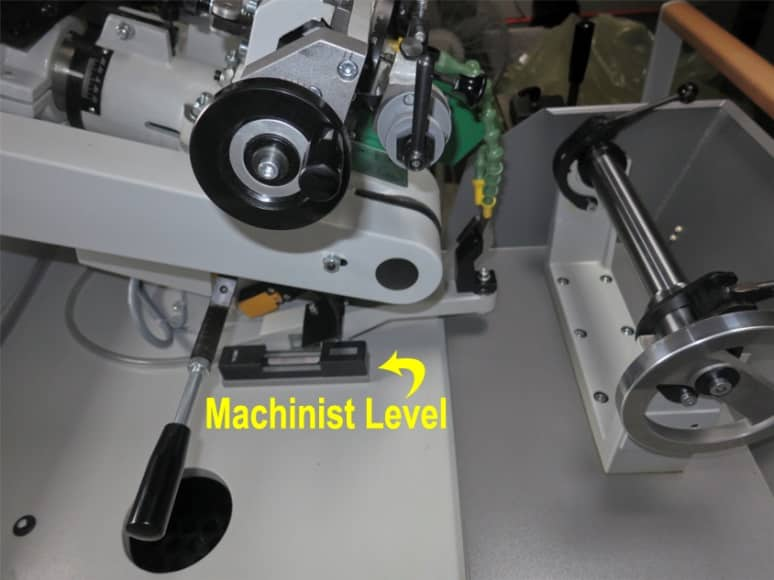
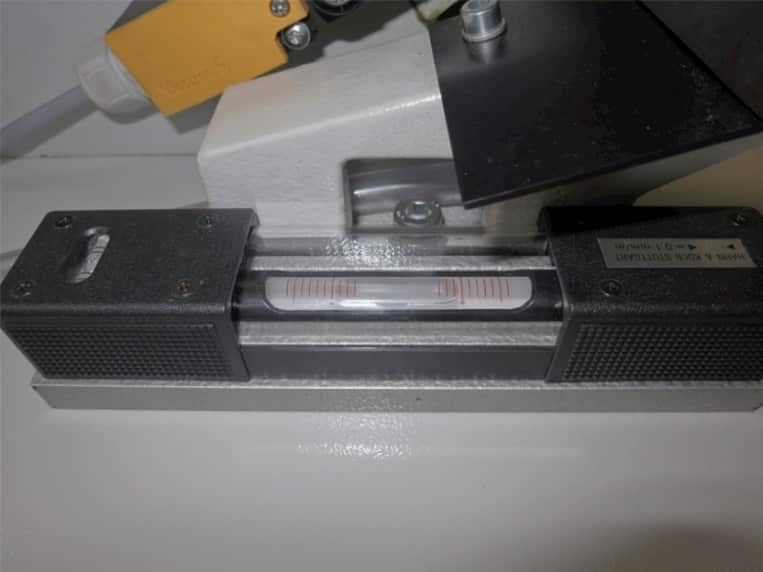
The final technical steps are as follows, check once again in each direction as illustrated to fine-tune the adjustments made earlier, lastly lock all the 19mm nuts in place using two wrenches, one on the 19mm nut on top and one on the 19mm nut below (see first image), this action will keep from moving the 19mm adjusting bolt.
We trust we have helped you accomplish the simple but important task of leveling your profile grinder with minimal effort, please check the level of your profile grinder and moulder periodically to assure levelness of all machinery owned.
We have other important profile grinder informational articles located on our website for your convenience, if we can be of any further assistance with any of these subjects please feel free to contact us.