The topic of moulding production has the potential to teach many valuable lessons in information and labor for your career as a developing moulding machine operator. You may have obtained information from trade/vocational schools or colleges attended, teamwork with other moulder operators, field service technicians, or maybe you were fortunate enough to work for a moulding machine manufacturer.
The information contained in this article enlightens on a just few of the tips we observed throughout our career in the woodworking industry. These helpful additives, not intended to change the way your company operates their moulding production; those decisions best left up to the production management staff. These are just a few constructive ideas, in some cases sometimes things that can otherwise be overlooked, these suggestions will increase yield, save time, boost morale, and keep your moulding knives sharper for longer intervals.
- By keeping, a small cut off saw near the in feed table enables you to cut off split ends of lumber that might otherwise tend to overlap or ride on top of each another during the feeding process of production, this could save potential moulding knife breakage or moulding machine damage.
- Use this saw to cut off the butt ends of lumber that might have staples or debris in them helping increase moulding knives production time by not having to sharpen you’re moulding knives as often.
- When using the process of blowing off lumber, compressed air will remove any debris that may have accumulated onto the lumber products while it sat dormant, this task taken outdoors will accomplish superior results.
- We recommend removing the top surface layer of the boards from a stacked unit of lumber and run it last. Debris will be present if lumber was stacked on top of the unit, forks from forklifts may have embedded warehouse fragments or dirt into top layer of the planks. In general, the manifestation of rubble destroys your nicely sharpened moulding knives. By running these pieces last your production run time will increase between moulding knife re-sharpening. The bottom layer of wood will be the same or worse, when the forks from the fork lift pick up the unit of lumber the debris present on the fork embed themselves into the planks.
- While milling lumber, especially hard maple, look for the dark black steaks known as natural mineral streaks. Mineral streaks occur when water that is utilized by the tree for nutrients contains minerals from the soil, as the water is drawn up through the root system and trunk higher into the leaves the minerals contained in the water become too heavy and are deposited into the lumber as seen below. Mineral streaks are tough on tooling; they will knick your moulding knives immediately, like hitting a rock, leaving drag marks on the lumber. To save yourself some time and increase your production, place this lumber aside and run it last.
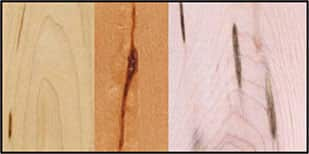
- Lumber containing excessive amounts of bowing or cup in them require a shorter length to eliminate the bowing. Cutting a board in half will increase the yield. Your moulder straightening fence will only do so much straitening based on the amount extra dimensions you left on each side of the rough sawn lumber. Common sense comes into play here; it is irresponsible to cut the boards in half if you are manufacturing eight-foot door or window jamb stock.
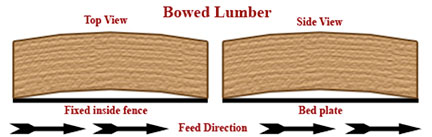
- Fabricating and installing a moulding off fall table to receive moulded lumber when it leaves the moulding machine allows the moulding operator to feed, catch, and stack on a five spindle-moulding machine, ensuing that you save labor costs. A six spindle moulder will be a slightly more of an overall challenge, a return feed system might serve as an enhanced alternative.
- Placing padded fatigue mats on the floor, especially in in areas where there is a higher volume of floor traffic, it is significantly easier on your feet and you will not feel as exhausted during the day.
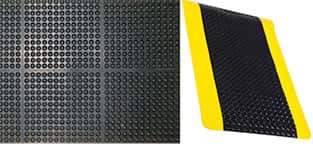
- Sharpen all straight moulding knives as they obtain approximately 2000 lineal feet. These straight moulding knives, often neglected, can transmit finish problems into other machining phases on the machine initiating finish issues on your milled lumber.
- Please, dedicate some time for maintenance each week, the last hours of the workweek is an effective time. Clean inside and underneath moulder, perform any needed maintenance, and look over the machine thoroughly, simultaneously, observing anything that does not have the appearance or feeling of a normal moulding machine operation. Dedicating this time and completing these task will allow you to come back to work on Monday and begin immediately with a well-maintained clean workplace.
- It is highly recommended that you check the calibration of all of your axial and radial counters on your moulder machine at least once per month. These standardization practices will assure you a rapid and accurate setup, conserving valuable pieces of lumber consumed during molder setup procedures.
- Fabricate a method of protecting and storing your collection of moulding knives that is quick, easy to find, this will save you a lot of valuable time during the molder setup process.
Our objective is to create an environment that is safe, effective, and optimized for milling professional mouldings that will surpass all others in their entire aspect. If you have, any questions or comments please feel free to contact us.